Offshore wind is now a fully global industry. It is well-established in Europe, with a number of high-profile wind farms already fully commissioned. In the wider APAC region, the likes of Taiwan, Japan, South Korea and Australia are ramping up activity, while China has almost as much installed capacity as the rest of the world combined. The US, which had been lagging behind, not only has a number of projects in development but also lease sales in frontiers such as the Gulf of Mexico and California.
While an uptick in wind development is vital in the move towards renewable energy sources, the sheer speed at which these projects are expected to be developed is likely to result in additional obstacles. Limited domestic manufacturing in emerging markets, a global undersupply of vessels and developing technologies outpacing infrastructure will all present unique problems as countries and developers strive to meet ambitious 2030 targets.
Highly accelerated growth means that the industry is on track for a supply chain crunch if solutions are not found. A supply crunch would mean not only costly delays in the offshore wind industry but also impact other industries which share the same infrastructure and vessel supply.
Note: The following analyses forecast the development of the global offshore wind industry, excluding China.
The global project pipeline: bottlenecks for the offshore wind supply chain
Spinergie forecasts approximately 270 GW of offshore wind capacity (fixed and floating) to be operating by the end of 2030 (excluding China) – only one-tenth of which is currently operational. The latter half of the decade is expected to do the majority of the heavy lifting, with more than 80% expected to come online between 2026 and 2030.
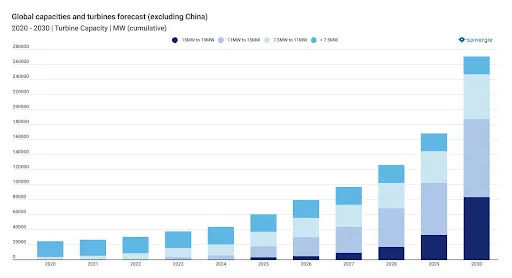
The North Sea (including the Baltic Sea) will continue to maintain its lead accounting for 179 GW, or two-thirds of the 270 GW, of the operational capacity by 2030. The frontier markets of North America and East Asia follow, with capacities of 22 GW and 21 GW respectively.
While fixed-bottom projects will remain dominant, representing 84% of the 2030 capacity, the number of floating wind farms is expected to rise rapidly to account for 16% of this capacity (up from almost 0% today).
Here, Spinergie has outlined the following issues as some of the main potential causes of supply chain bottlenecks. A global increase in bottlenecks, whether through a lack of vessels, overloaded fabrication yards or availability of quays and areas used for marshalling bases, could see projects delayed and deferred well into the future and past the major capacity targets outlined for 2030 (including 60 GW strategy guideline in the EU; 50 GW in the UK, 4.5 GW in Norway and 30 GW in the USA). It should be noted, however, that a number of countries within the EU have since announced more ambitious targets and the true picture is now well beyond the official 60 GW guideline at 109 GW of target capacity.
On top of the challenges in meeting these targets, bottlenecks are also likely to cause increased transport costs and carbon emissions.
Crucial challenges faced by offshore wind developers
Global Expansion
Outside of China, which is closed off to foreign players, Europe is currently the busiest market in the offshore wind market, however, a shift is expected towards newer markets and larger-scale projects in Asia and the USA. Larger capacity projects will mean additional factory time is required for building more components and more vessel time will be required for transport and installation activities.
The impact of weather within each global region cannot be understated. Projects in regions such as the North Sea and parts of the US or Australia will be subject to weather windows as installations will be unable to go ahead in the harshest conditions. It is also important to note the region-specific fauna behaviour that also has to be taken into account. A key example of this would be the whale breeding season off the US east coast, which puts a pause on any offshore construction. With installation in various locations restricted to only a few months, including vessel transit time, it adds an additional logistical burden for developers to work around.
Vessel undersupply
A significant number of heavy load carriers/general cargo vessels and heavy lift installation vessels will be required to enter the wind installation market to meet projected demand. In key markets, it is also important to remember that many vessels are shared between the offshore wind market and oil and gas. With oil and gas still an active market, and some regions facing increased demand, there will likely be a supply crunch in the support vessels covering all industries.
In a close analysis of one recently commissioned wind farm off the northwest coast of France, Spinergie uncovered the exact number of vessel days required for supply and installation for that specific project in terms of general cargo and heavy-lift installation units.
Overall, 739.5 vessel days were required for supply, using six vessels, however, this has a number of exclusions including array cable transport; inland transport for the monopiles, primary steel and transition pieces; and road transport for the remaining nacelles. Installation took 981 vessel days with the monopile foundations taking 391 of those days.
In all, a total of 1,720.5 vessel days were required for the supply and installation of the wind farm with general cargo/HLC vessels taking 81.25% of all vessel days by carrying all the turbine and foundation components. Recent Spinergie analysis of utilization within the HLC fleet of one vessel manager showed that it reached an average of 60% per year - peaking at 80% - which indicates that this market segment is already particularly busy.
In understanding the number of vessel days required for a project it is clear to see where bottlenecks may arise. Following this example, general cargo/HLC vessels will see high levels of demand, especially as distances between wind farms, logistic ports and manufacturers increase.
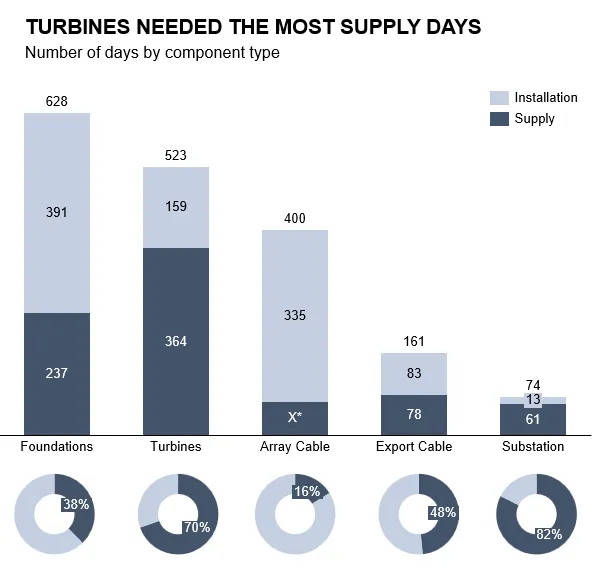
In the wider wind market, the US Jones Act is a good example of how vessel supply can be impacted. It is clear that the number of key vessels required in wind farm construction must rise, especially wind turbine installation vessels (WTIVs) to meet upcoming US demand. The Jones Act adds an additional layer of complication for developers within the US region. While cable layers, pipelayers and rock installation vessels are able to perform activities without being Jones Act compliant, all other vessels, including WTIVs, are not exempt. While in rare cases, such as defence or in natural disaster recovery, waivers may be granted to non-Jones Act-compliant vessels, and in theory, this would include WTIVs, in reality, it is improbable that wind installation operations would fall under the waiver requirements. As it stands, only one WTIV is Jones Act compliant: Dominion’s Charybdis. Three more units remain under discussion but no firm contracts have been signed.
Meanwhile, however, there are some indications that vessel conversions can be utilised for the offshore wind market: jackups and drillships from the oil and gas industry can be converted into wind installation vessels, Bokalift 2 (the ex-GSF Jack Ryan drillship) being a recent example, and PSVs can be converted into SOVs. However, it is unclear whether these conversions will be suitable long term. While the vessels are suitable for current offshore wind technology, they may not keep up as technology trends larger. Therefore, new vessels will need to be purpose-built to meet the demands of bigger turbines and supply chain components long term.
Changes in technology
The previous point leads to further implications from technological advances in offshore wind. As wind farms are trending bigger, both in terms of scope and component size, it is important that the infrastructure used for these projects is also capable of growing in size. This could look like developing deeper ports for example, especially in light of increasing floating wind projects. As the number of larger floating wind projects increases, so must the ports' infrastructure to accommodate them. Hand in hand with the onshore infrastructure needed to accommodate new offshore wind technologies and larger components, specialised vessels will also be required.
Lack of domestic infrastructure
In the previously mentioned French offshore wind farm analysis, Spinergie identified 11 European project sites involved in its supply chain including three ports to handle the logistics of arriving components. With the number of projects multiplying and the relatively limited infrastructure within the region, it is clear that high numbers of wind farms all using the same amount of infrastructure could result in bottlenecks if not managed.
More logistical bases and ports must be established to meet upcoming demand, especially with the unique challenges of floating wind. Port tests have been undertaken in the North Sea for floater storage and assembly, however, while tests ran smoothly it is unlikely to take on a full-scale project. A number of North Sea ports, led by Esbjerg in Denmark, have created a partnership to resolve the capacity issues the region is already seeing. Such partnerships in other regions, especially those without infrastructure currently in place, could prove key as collaboration gains importance in meeting targets.
In the US, the issue of domestic infrastructure is compounded further as there are very few existing ports on either the east or the west coast that are capable of supporting offshore wind operations. Change is already underway, however, as the NREL indicates that additional investments have been planned for the development or expansion of 12 US ports.
Limited domestic manufacturing in key markets
The US market, due to currently only having one major facility in operation, expects that in the near-term most components will be sourced from Europe. Europe has, however, already begun to look towards Asia to provide components as fabricators struggle to keep up with booming demand.
Meanwhile, to alleviate some pressure from the burgeoning US market, the NREL states that plans to build at least 11 new domestic manufacturing facilities are in place. These new plants will include facilities for blades, foundations, towers and cables. However, the NREL has also identified a number of subcomponents that will “continue to pose a challenge to domestic manufacturing because of their size or speciality.” Such components include flanges and other large cast or forged components, electrical systems for offshore substations and mooring chains. Therefore, while work is underway to alleviate the pressure in some regards, there are not yet indications it will be reduced entirely.
Conclusion
While the path ahead will clearly be challenging, and developers will have many logistical concepts to work through regarding the supply chain, government measures have been introduced to alleviate some pressures, particularly in terms of funding. In the EU and the UK, this includes a number of subsidies and support initiatives including Horizon Europe, the Contracts for Difference scheme and the Offshore Wind Investment Programme. In the US, the Biden administration has put in place a series of programmes and funding opportunities for floating wind in particular, with hopes to reduce the costs of floating wind turbines in the region by 70%.
The fact remains, however, that the targets put forward for 2030 are ambitious, especially with just under seven years left to go before this deadline. As the offshore market will continue to grow beyond 2030, it is important to have these initiatives in place as soon as possible to meet all of the potential demand and ensure the threat of bottlenecks in the supply chain is reduced as much as possible.
As the wind supply chain tightens, every step will be impacted from the planning stages, through to development, transport and construction then onwards into operation and maintenance. Analysis of the supply chain, leading to increased knowledge of where optimisation will occur is crucial as the industry progresses towards wind capacity targets.
Read more: How Spinergie’s analysis can track potential offshore wind supply chain difficulties
Contact Spinergie today for a demo on how our analytics can help you track and monitor ongoing wind farm operations and uncover optimisation opportunities for your general cargo fleet.