By year-end 2023, cable laying vessels (CLVs) had installed 2,345km of cable across various industries ensuring a record year. The length of cable laid, the first time the 2,000 km marker had been reached, was over 650 km more than in 2022 and almost double the volume recorded in 2017. According to Spinergie analysis, the strongest growth in the cable market has been in wind farm export cables, with a 33% increase in 2023 compared to 2022.
Further growth in the subsea cable industry is anticipated, and contractors have reacted accordingly. At least 11 newbuild cable layers are on order, with three of those units already having work lined up, the first from mid-2026. This is in addition to the four newbuilds that have been delivered to the market since the beginning of 2022.
While the market is booming, however, it is crucial to consider additional strains on fleet time, including cable failure. Here, we examine how subsea cables fail and how repairs are performed.
Note: Array cables and telecom cables were not included in the study.
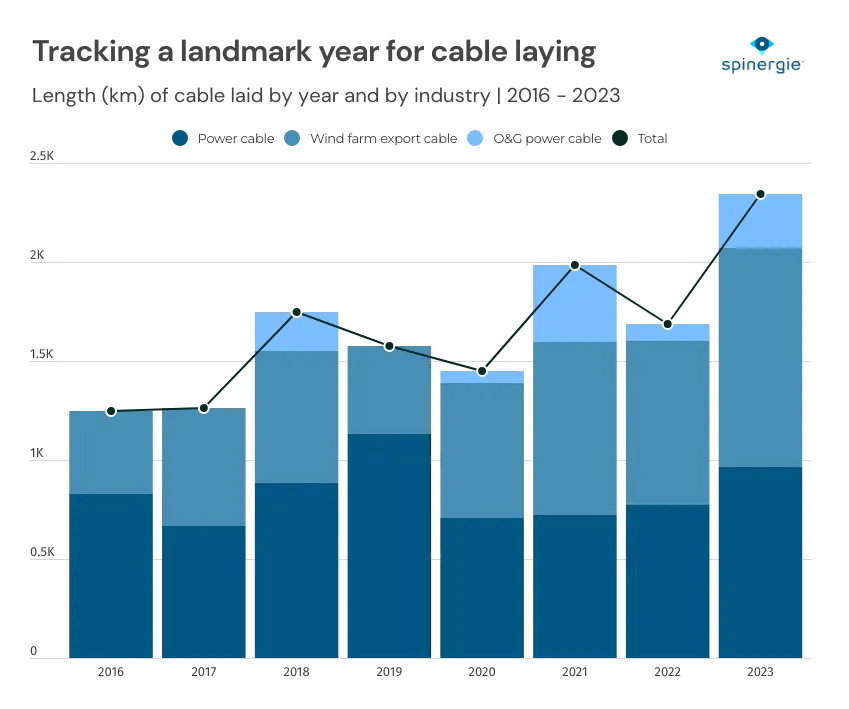
Unveiling the internal and external causes of cable faults
There are a variety of factors that can cause cable faults, ranging from issues that arise during the manufacturing phase to those that show up later through accidents or mishaps.
Installation and Exposure
There are two types of issues that can arise during installation that are most likely to cause failure at a later date. Mishandling during the installation process is the first potential issue, and this can arise via damage sustained from tools and equipment, a kinked cable, or bird caging - which is a type of distortion that sees the individual outer strands of a cable unravel and expand to ultimately create a bird cage shape at the damaged area.
Exposure is also a key factor and can arise if the cable is unprotected due to currents or if there has been insufficient seabed preparation or reduced visibility during cable laying operations. Exposure then leaves the cable vulnerable to abrasion and external damage.
Fishing and Anchors
Fishing activities pose a significant risk to subsea cables. Fishing gear, like trawlers or nets, can snag and damage the cables, leading to mechanical failures. Ship anchors are another common external cause of failure, as their being dragged across the seabed has the potential to displace or sever cables.
Manufacturing and Misuse
Faults can be caused even before installation. Cables with manufacturing defects can experience corrosion more easily and may also be subject to thermal issues surrounding cable insulation. Finally, when the cable is in use, inadequate power or defective insulation can lead to overheating, which, in turn, compromises cable integrity because the cycle of overheating followed by cooling results in damage.
How cable faults are found
- Failure Location: At the earliest stage, measurements are taken from the substation in order to estimate the location of the failure. Once this general point is located, a construction or survey vessel with an ROV is deployed to find the exact point of failure. In some instances, this process can take months, as was the case with the Basslink subsea cable failure in late 2015. Ultimately, the fault was discovered and was likely caused by the heating and cooling of the cable under operational stress, but this process lasted into late 2017.
- Preparation: Next, the faulty cable section is cut, tested, and removed. The cable ends are then sealed to prevent water ingress and hooked up to buoys.
- Mobilisation: An available CLV is then sent to the operations base. Replacement cables and joints are loaded from storage.
- Repair: In the final stage, cable ends are recovered. The first-in-line joint connects one cable end to the replacement, and jointing is performed at the other end. Finally, the repaired cable is laid back on the seabed.
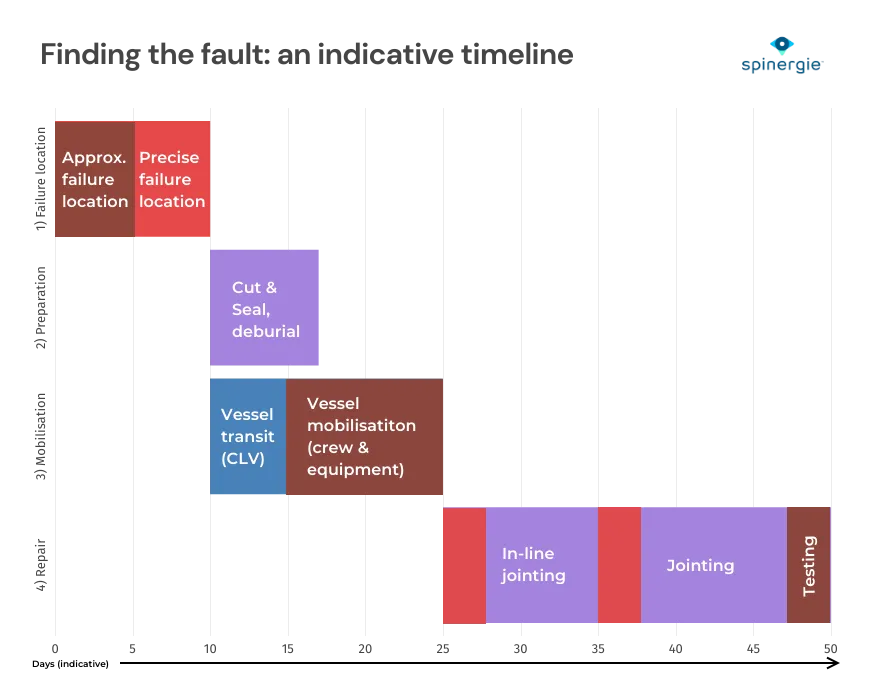
Read More: New challenges lay ahead as demand for offshore cables increases
The market impact: an analysis of cable repair activities
The short-notice mobilization of CLVs and construction vessels (CSVs) for just a few weeks at a time to deal with subsea cable failures can be significantly disruptive, hindering both the efficiency and cost-effectiveness of power infrastructure. Spinergie analysis has observed that, since 2016, there have been 149 subsea cable repair activities across 97 different cables. This includes wind farm export cables, oil and gas cables, and interconnectors.
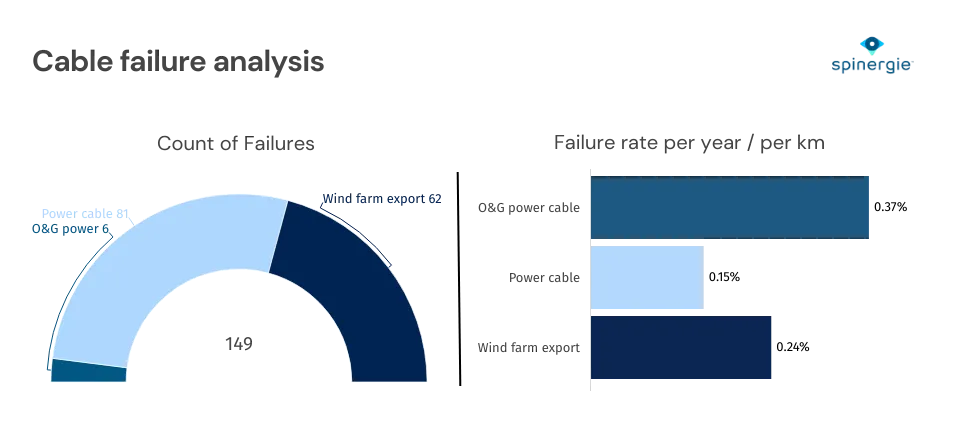
Analysis indicates that power cables had the most repairs overall, but this category also saw the least amount of repairs compared to lifetime and length. This suggests that the depth and remoteness of interconnector-type cables can lower the chance of external damage, one of the most common causes of failure.
In wind farm export cables, the average rate of failure is 0.0024 failures/year/km, which means a wind farm with 100km of export cable has a 24% chance of cable failure in any given year. The cumulated probability of failure would reach 95% in 11 years.
While a cable could go years without a failure, some cables suffered more than others, a key example is the Malta-Sicily Interconnector, which was damaged twice in two years.
Case Study: Malta-Sicily Interconnector
The Malta-Sicily interconnector, operated by Enemalta, was commissioned in March 2015. Manufactured by Nexans, it is 94.7 km in length (220kV HVAC) and is laid in water depths between 14 and 160 meters.
Cause of the Failure
The interconnector, a power link between Malta and Sicily's power grid, was damaged in December 2019. Two of the three conductors and all fibreoptic lines were damaged. The primary cause of the damage was identified as a ship's anchor, cutting the cable in two at a depth of 150 meters, with Singaporean-flagged oil tanker Di Matteo the culprit. The cable was situated on a sandy seabed, where it could not be trenched but was instead laid using a jetting process.
Response and Repair Process
In early January 2020, Nexans mobilized the construction vessel Argo (then Polar King) to inspect the cable damage. An ROV located the exact damaged spot. The damaged part of the cable was exposed by Argo using a water-jetting system.
In mid-February, Asso.subsea's cable repair vessel Ariadne was mobilized from Athens to Malta to begin loading the spare cable. CLV Atalanti also participated in the repair process. The damaged section was cut out, and the ends were sealed in preparation for the repair. In mid-March, a spare cable was spliced in at the damaged area. After the splicing, the interconnector was re-energized, restoring the connection.
The Argo returned in late April to trench the repaired cable section to a depth of approximately 1.5 meters.
Economic Impact
The repair contract was valued at €11 million, with repair vessels mobilized for a combined 54 days. Enemalta's contingency plan during repairs involved powering all available power plants at a cost of around €150,000 a day.
In March 2022, the anchor of another tanker, Chem P, damaged the same cable again during a storm. This time, Nexans Aurora was sent on the repair mission in November, with operations taking 20 vessel days.
Conclusions
The escalating demands of the offshore wind industry underscore the critical importance of understanding cable repairs in the maritime sector. The surge in offshore wind projects has significantly increased the need for vessel days dedicated to cabling operations, prompting a reevaluation of existing resources. While there are newbuild vessels on the way, there is likely to remain a strain on the current fleet for the foreseeable future, emphasizing the urgency of efficient and streamlined repair processes.
Cable repairs involve addressing multiple factors that can be disruptive to the fleet, necessitating a strategic approach. Additionally, a proactive stance on cable fault prevention is crucial. This involves a comprehensive understanding of how cable faults develop, enabling preemptive measures to mitigate risks where possible. Learning from previous repair missions provides invaluable insights, helping the industry adapt and evolve in response to a progressively busier market.