When offshore wind turbines fail, for technical or environmental reasons, heavy maintenance is usually the next step. Yet maintenance programmes bring challenges of their own meaning developers must plan around component lifecycles, balancing risk and proactive maintenance, to avoid too much disruption.
As global offshore wind capacity grows, understanding failure patterns becomes essential for optimizing operations and ensuring long-term project viability. Here we examine the causes behind turbine failures, their impact on the market and future expectations.
What are the main causes of failure in offshore wind turbines?
Heavy maintenance interventions in offshore wind turbines typically involve replacing or repairing major components (aka Major Component Replacement, or MCR) such as gearboxes, main shaft bearings, generators, pitch bearings, and blades. Gearbox failures are frequent, affecting nearly half of geared turbines over a lifecycle of 20-25 years, and main bearings replacements are common.
Blade replacements, although less frequent, can be significant in some wind farms due to weather-related damages like lightning or erosion. Pitch bearing failures occur regularly due to mechanical stresses, requiring complex blade removal.
Generator replacements are critical and can require a complex offshore operation in direct drive turbines, though relatively less common at this stage.
These failures all contribute to maintenance needs, production downtime, and operating costs.
What factors increase failure rates in offshore wind turbines?
While environmental conditions, design issues, and scaling of turbine size can all increase failure rates, aging is the strongest predictor. Aging turbines naturally experience component fatigue, increasing the likelihood of failures after around six to seven years.
Harsh offshore environments, such as exposure to saltwater, high winds, storms and lightning strikes, all accelerate wear and lead to higher failure rates.
Design flaws can cause serial issues across multiple turbines of the same model, such as gearbox or blade manufacturing faults. Additionally, the trend of scaling up turbine size introduces new failure risks due to larger, heavier components facing greater mechanical stress.
How are operators impacted by wind turbine failure?
Heavy maintenance failures affect offshore wind operators operationally and strategically. Operationally, these interventions cause prolonged downtime, reducing electricity production and revenue, which is especially problematic during high wind periods.
Repairs often depend on limited vessel availability and suitable weather windows. This further extends downtime and increases logistical complexity. Strategically, developers must plan meticulously around component lifecycles. They need to decide whether to perform preventive replacements or accept risk, and structure O&M contracts and insurance to manage heavy maintenance uncertainties.
Long-term, failure patterns shape investment decisions, technology selection, and the overall economics of wind projects.
Jack-up interventions in offshore wind heavy maintenance
Planned maintenance, predictive monitoring, and actual failures all trigger jack-up interventions. Operators weigh component condition, urgency, weather forecasts, vessel availability, and downtime costs when scheduling these repairs.
Contractually, interventions are covered by long-term O&M agreements, either fully outsourced to OEMs through service agreements or handled directly by the operators through self-managed strategies. Key actors involved include turbine OEMs (e.g., Siemens Gamesa, Vestas, GE), wind farm operators and marine contractors.
The Jack-Up fleet involved in heavy maintenance
Jack-up vessel owners are largely divided between dedicated heavy maintenance contractors and those primarily involved in installation campaigns. Currently, two players, Ziton and Harren & Partner, dominate the offshore wind heavy maintenance market, accounting for around 60% of the total maintenance activity in a steady trend over the years.
Ziton's fleet is exclusively committed to O&M, while Harren & Partner's is diversified across additional sectors. The remaining volume is tackled by diversified wind contractors, such as Van Oord, DEME, Jan de Nul, and Cadeler, which mainly focus on installation contracts but occasionally perform spot O&M contracts as well.

The heavy maintenance fleet sees continued high utilization
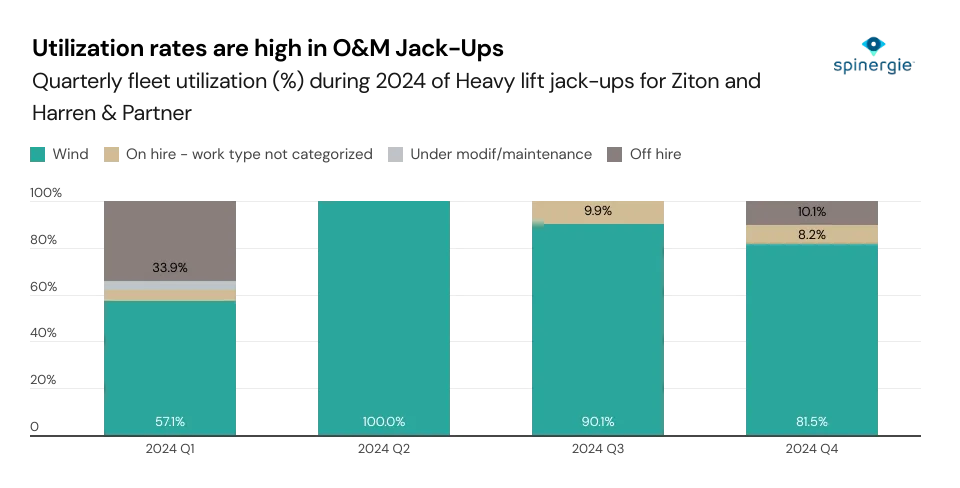
O&M jack-ups have very high utilization, averaging ~80% per year. Such high utilization rates are achievable because heavy maintenance vessels benefit from stable, recurring demand driven by aging offshore wind turbines and preventive maintenance schedules.
Unlike installation jack-ups, which face project delays or seasonal downtime, maintenance jackups like Ziton’s assets maintain high utilization through long term O&M charters with turbine OEMs.
What do we know about intervention rates to date?
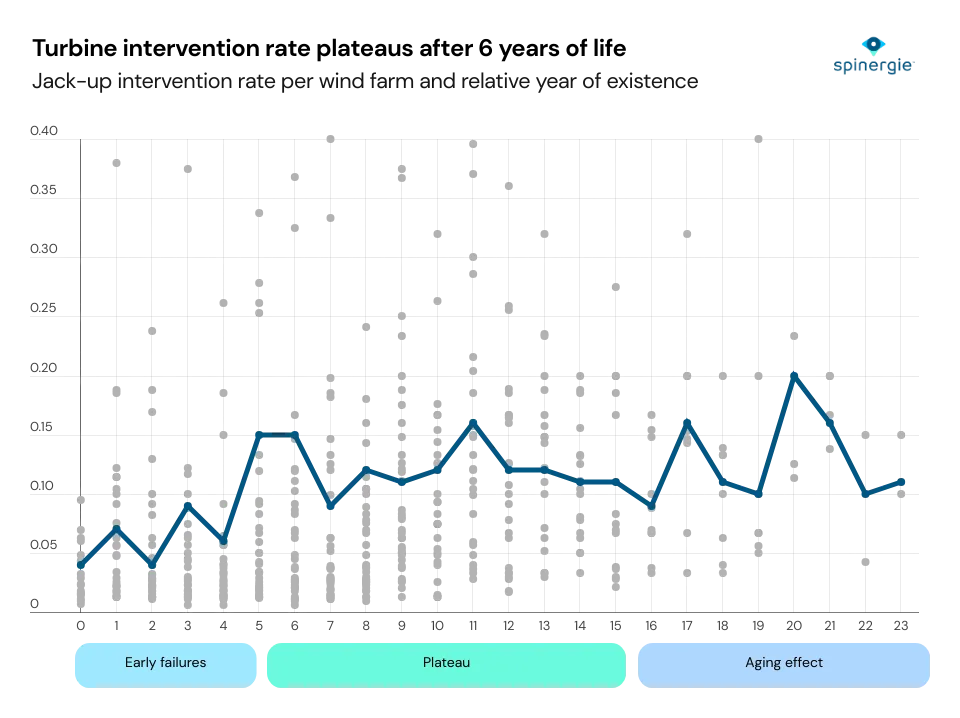
Spinergie analyzed 3,400 unique jack-up interventions on turbines worldwide and extracted intervention rates per year of wind farm life. The chart reveals a pattern where jack-up intervention rates rapidly increase during the initial six to seven operational years of offshore wind farms, likely reflecting early-life component failures and defects.
After this initial rise, the intervention rate plateaus, stabilizing with only minor growth attributed to gradual aging of turbine components. This plateau indicates that after overcoming initial reliability issues, wind farms experience relatively consistent heavy maintenance needs.
The following upward slope suggests component fatigue and cumulative wear become slightly more influential as the wind farm ages beyond 15+ years old. At the turbine model level and at the turbine size levels, disparities were observed, with some models appearing more often than others.
Europe continues to dominate intervention demand
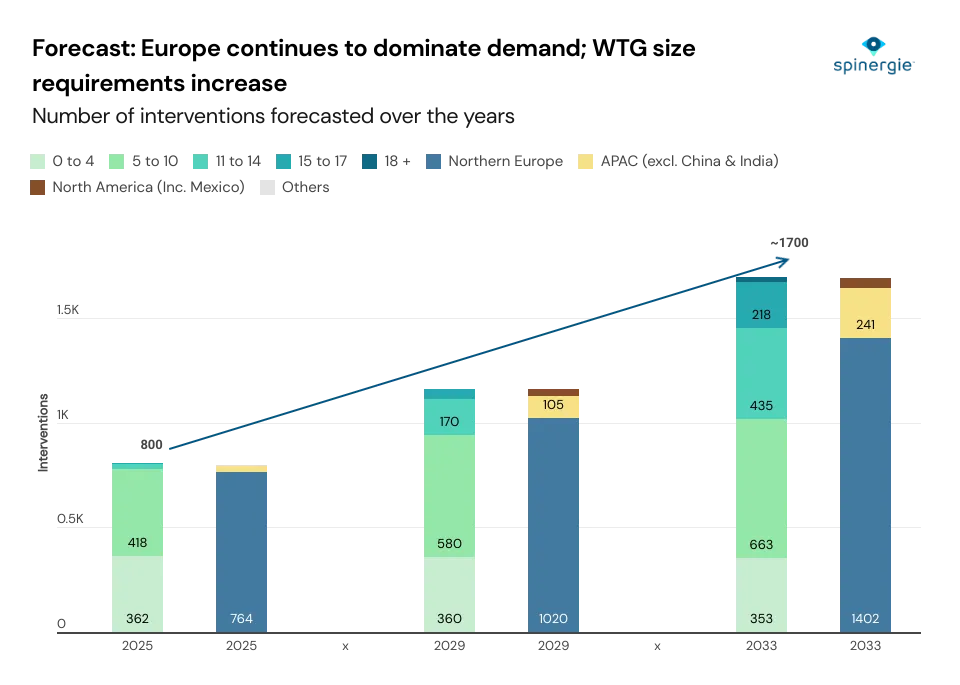
The forecast shows a continued rise in global jack-up intervention demand, with Northern Europe maintaining the highest volume throughout due to its large, growing and aging turbine contingent. The share of interventions from APAC grows rapidly—more than doubling from 2029 to 2033—as offshore wind capacity expands across Taiwan, South Korea, and Japan.
North America demand scales in a more sustained manner by 2033, driven by the maturation of U.S. wind farms currently under construction, such as CVOW or Vineyard Wind 1. Due to the Jones Act, Dominion Energy's Charybdis will be the top choice to service these turbines, or the maintenance will need to be executed from Canadian ports. As the earlier wind farms built in Europe in the 2010s get decommissioned or repowered in the 2030s, the share of small turbines wanes. In parallel, a large share of 15 to 17 MW turbines would require maintenance, ramping up from representing only a marginal share of the 2025 demand.
Overall, JU interventions would jump from an estimated 800 in 2025 to ~2100 in 2037, growing 9% per year on average. The increase in maintenance time will compound the growth of maintenance numbers, making demand for JU vessels rise even faster. This will prompt fleet expansion from maintenance players, along with bringing opportunists to consider more sustained O&M businesses.