Global supply chain pressures are at the forefront of offshore wind players' minds. With capacity targets ramping up in most regions, there continues to be a lack of the infrastructure, vessel availability, and manufacturers needed to support this increased demand.
Read More: What is driving global wind demand, and are ambitious global capacity targets attainable?
While indicators of a supply crunch are clear within the global market, a close analysis of atn existing, commissioned project has uncovered some important learnings surrounding the global supply chain. By taking heed of these learnings, developers and other stakeholders can plan better and adapt to the challenges ahead while mitigating the potential for supply chain disruption in their projects.
Case Study: What can the offshore wind industry learn from the supply phase of Seagreen 1?
Seagreen 1 is a joint venture wind farm developed by SSE and TotalEnergies off the coast of Angus, Scotland. With a capacity of 1,075 MW generated by 114 turbines, this is Scotland's largest offshore wind farm and became fully operational in October 2023. This project stands out for its innovative approach, utilizing Suction Bucket Jacket (SBJs) foundations.
During this campaign, the project achieved a groundbreaking feat by installing the deepest ever offshore foundation, reaching a water depth of 58.6 meters. Here, we examine this project's supply chain impact, which lasted 28 months.
Key Learning #1: Supply plays a massive role in the number of vessel days attached to a wind farm project
Supply began three months before the start of the installation campaigns when components began to be stored in the port of Nigg, northeast Scotland, awaiting the installation vessel. In total, 11 Heavy Load Carriers (HLC) were mobilized, notably for 25 trips from Asia to the UK, each lasting around two months. More than 3,100 vessel days were needed to transport foundations, the substation, and turbine components from their factory to their marshaling port.
Key Learning #2: A large number of fabrication and marshaling ports are required
The supply chain for Seagreen 1 spanned three continents: North America, Europe, and Asia. All three marshaling ports were located within the UK, but the fabrication facilities were further afield, aside from those in the UK, Norway, Denmark, and the Netherlands. The foundations had to be transported from two facilities in China and another in the UAE.
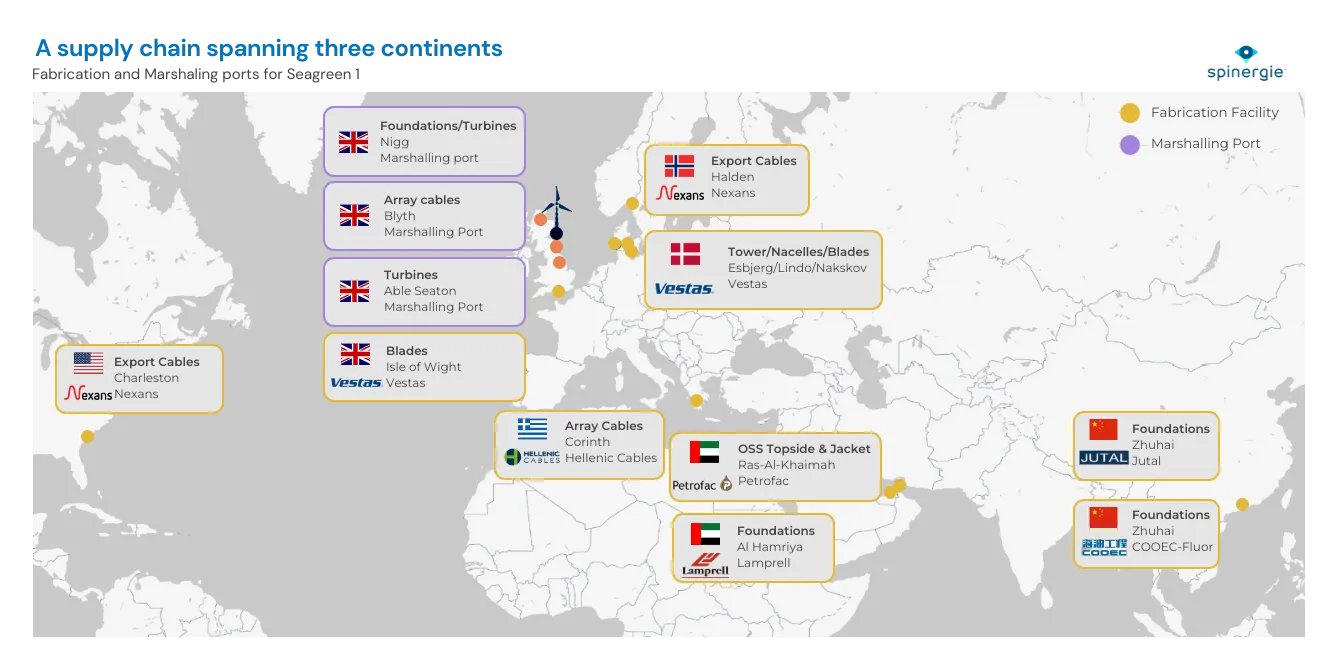
Key Learning #3: Four times more vessel days were needed for supply compared to installation
The various manufacturers of Suction Bucket Jacket foundations all have a background in the oil and gas industry and are, therefore, specialists in constructing jackets. The supply of all 114 jackets took 2,473 vessel days in total, while their installation took 330 days. As the turbines were locally supplied, the vessel days needed for their transport were lower, about 500 days.
During the turbine installation campaign, two different marshaling ports were used: the port of Able Seaton for the first 72 turbines and the port of Nigg for the last 42. The port change can be explained by the fact that Able Seaton was to be the marshaling port for Dogger Bank A, and a replacement port had to be found.
Some differences can be noted between the supply of foundations and turbines. The turbine manufacturer, Vestas, charters their HLCs, Boldwind and Bravewind, which travel between the factories and the marshaling ports of the wind farms they supplied. As for the foundations, the supply chain seems less established, with many different contractors involved.
All 114 foundations of Seagreen 1 were transported from Asia to the port of Nigg using HLCs from five different managers. A total of 23 trips were carried out by seven different vessels. These vessels can carry five foundations at a time, each measuring up to 93 meters in height and weighing up to 2,250 tons.
The first Suction Bucket Jacket was shipped from China to Nigg in June 2021, while the last arrived in Nigg 18 months later, in December 2022. Some vessels, such as ZOMC's Zhen Hua 33 and Guangzhou Salvage's Hua Yang Long, have transported SBJs from China and the UAE to the UK.
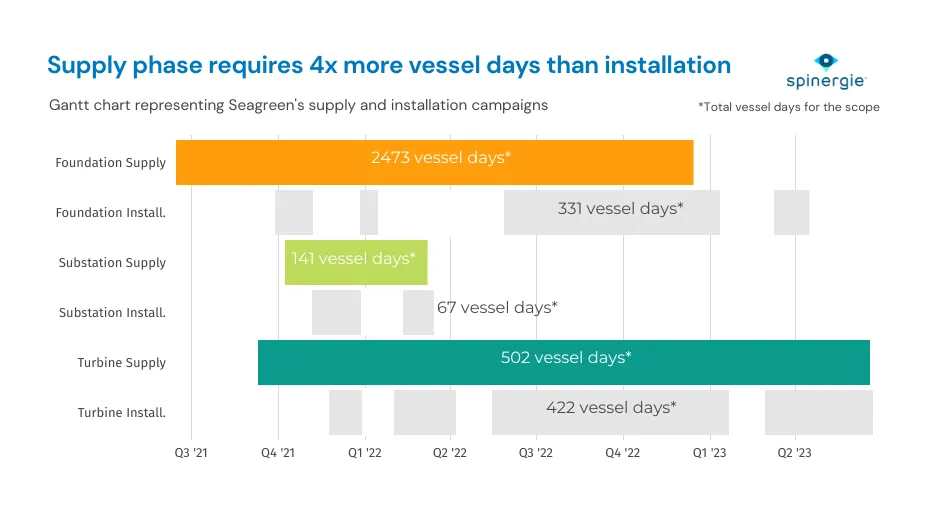
Key Learning #4: Many trips will be required by heavy load carriers during the supply process
Two HLCs were used in the European supply chain for the Vestas turbine components used at Seagreen 1: United Wave Logistics’ Boldwind and Bravewind. A vast number of components had to be transported, including 114 nacelles from the fabrication facility in Lindo, Denmark; 45 blades from the fabrication facility in Nakskov, Denmark; 297 blades from the Isle of Wight facility, UK; and 342 tower sections (three per turbine) from the fabrication facility at Esbjerg, Denmark.
Nacelles: HLC Boldwind transported 15 nacelles per trip in eight trips to Nigg and Able Seaton ports, both used as marshaling ports for Seagreen.
Blades: From Nakskov, HLCs Bravewind and Boldwind transported 15 blades per trip with five sets of three blades stacked on their deck across three trips. From the Isle of Wight, both HLCs were again used as most of the blades were manufactured in Vestas' Isle of Wight factory and transported to Nigg and Able Seaton from Portsmouth, UK. This portion was undertaken in 20 trips.
Towers: In 23 trips, the tower sections were transported from Esbjerg, Denmark, using Bravewind and Boldwind and assembled once in Nigg and Able Seaton.
Key Learning #5: Even in mature markets with domestic infrastructure, there is a global element
Cables supplied from the USA and Europe
Seagreen 1 is connected to the UK grid via three 65-km export cables, two manufactured by Nexans in Charleston (US) and one in Halden (Norway). The Nexans Aurora CLV was used to transport the cables from the factory before installation.
Seaway's CLVs Aimery and Phoenix installed the array cables in three campaigns. The cables were manufactured in Hellenic Cables' factory in Corinth (Greece) and delivered in Blyth port (UK).
Substation delivered from the UAE
The 5,100-ton, six-legged OSS jacket was manufactured by Petrofac in the UAE and transported with its six piles by HLC Dongbang Giant No.8. The trip to Seagreen took 39 days, and installation was performed by Saipem 7000.
The substation's topside was supplied by Pan Ocean's HLC Sun Rise from Petrofac's Ras-al-Khaimah factory during a 46-day trip before being fed to Heerema's Thialf for the installation.
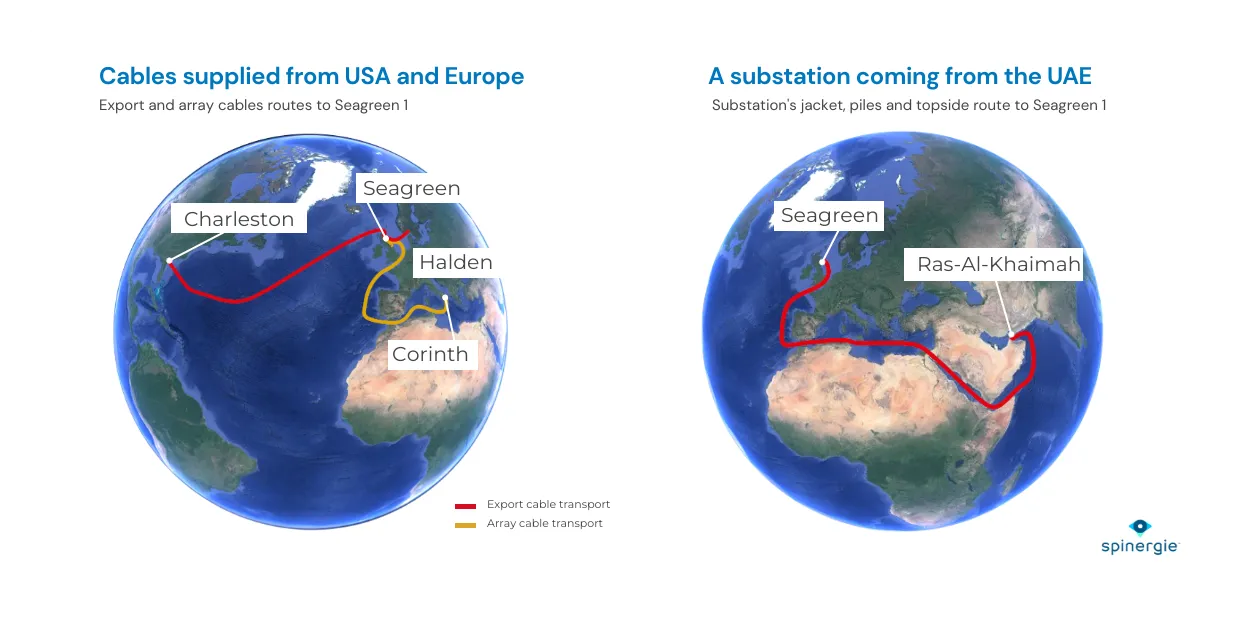
Read More: How Spinergie’s analysis can track potential offshore wind supply chain difficulties
Through this close analysis of just one fixed-bottom large wind farm development in the mature North Sea market, we have learned important lessons that can help shape future projects. With upcoming projects now spread throughout the globe, especially in upcoming markets with limited domestic infrastructure in terms of fabrication yards and marshaling ports, such as the U.S., it is crucial to consider these learnings when planning.
Additional reporting by Sarah McLean